How to torque diff flange nut?
#1


Thread Starter

What can I use to hold the diff flange in place while tightening the nut? (Yes, it's a new nut; also plan to use loctite.)
Oh, and should I bother replacing the oil seal?
Oh, and should I bother replacing the oil seal?
#3
Registered User

Join Date: Jan 2006
Location: 17 ft below sea level.
Posts: 4,949
Likes: 0
Received 21 Likes
on
16 Posts

Originally Posted by SgtB,Dec 1 2010, 05:40 PM
I'd replace the seal. I used a long section of angle iron with holes spaced to bolt it to one side of the flange.

On both

Replacing (and mounting) the seal is a little harder with the pinion in place (if that's what you're doing) but worth it.
If the diff is in pieces.. replace all seals.

#4


Thread Starter

Thanks guys, think I have some angle iron lying around somewhere. 
I do want to keep the diff in one piece; any tricks or special tools needed for the oil seal?

I do want to keep the diff in one piece; any tricks or special tools needed for the oil seal?
#5
Registered User

Join Date: Jan 2006
Location: 17 ft below sea level.
Posts: 4,949
Likes: 0
Received 21 Likes
on
16 Posts

IIRC the seal seals
on the flange, so you've got some room to pry without having to worrie about damaging a seal surface on the pinion.
Don't create any shavings that might fall in the bearing.
Be very carefull not to overtighten the nut on the allready crushed sleeve.
Use small steps and turn the pinion to seat the bearings every step.

Don't create any shavings that might fall in the bearing.
Be very carefull not to overtighten the nut on the allready crushed sleeve.
Use small steps and turn the pinion to seat the bearings every step.

#6
Registered User



Just pry the seal out with a flat head and drive the new one in. I used a very large socket to drive it even. You want to torque the nut until it takes 12in/lbs to turn the pinion freely. The helms has the procedure, and puddydad has a post on here about it.
#7


Thread Starter

Got it. Thanks again!

Trending Topics
#8
Registered User

Join Date: Jan 2006
Location: 17 ft below sea level.
Posts: 4,949
Likes: 0
Received 21 Likes
on
16 Posts

SgtB Posted on Dec 1 2010, 11:34 PM
Don't forget "the helms procedure" is done without the ring in place, just turning the pinion.
If you put bolts in the angle iron in the pitch of the flange holes and use them as pins (or fingers) its easy to hold the flange-tighten nut-turn flange-hold flange-tighten nut, etc.
You want to torque the nut until it takes 12in/lbs to turn the pinion freely. The helms has the procedure..
If you put bolts in the angle iron in the pitch of the flange holes and use them as pins (or fingers) its easy to hold the flange-tighten nut-turn flange-hold flange-tighten nut, etc.

#9


Thread Starter

Originally Posted by SpitfireS,Dec 1 2010, 09:05 PM
Don't forget "the helms procedure" is done without the ring in place, just turning the pinion.
What do you think?
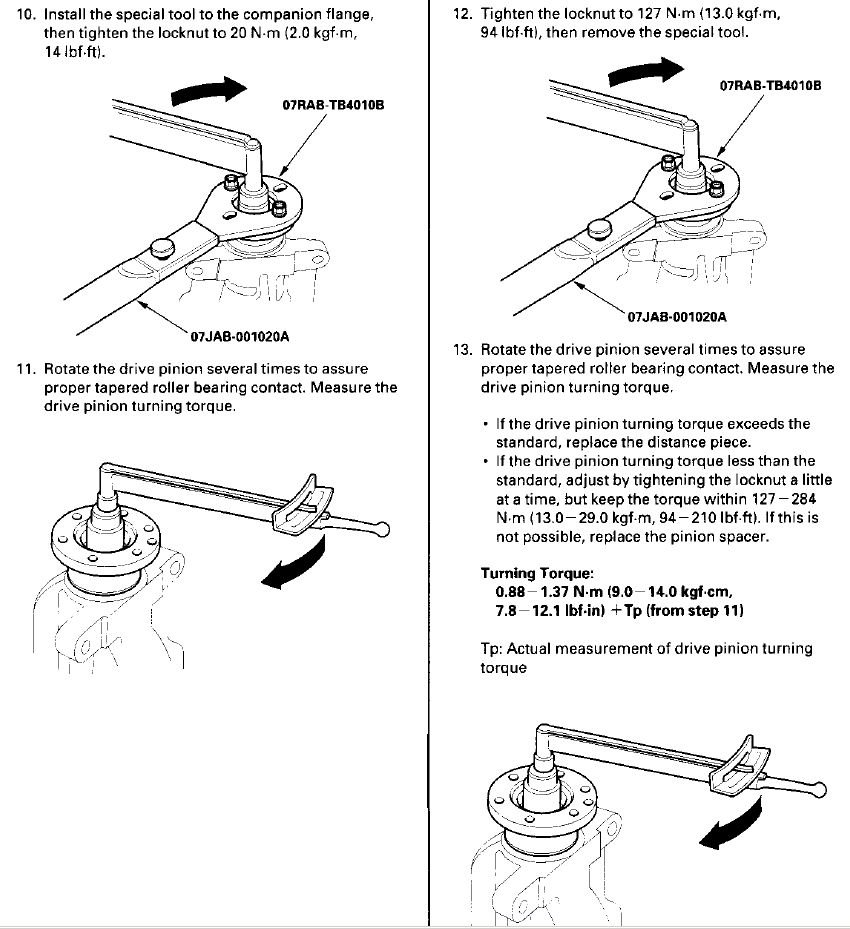
Last edited by twohoos; 12-01-2016 at 03:04 PM.
#10
Registered User



Good point. I must have interpreted that post incorrectly. I sort of went by feel anyway.
I was just swapping flanges and didn't separate the halves. I'm pulling it back apart soon to see how it's done over the course of a year.
