Half Shaft CV Joint Spacers at Standard Suspension Height?
#12


Join Date: Nov 2007
Location: Illnoise. WAY downtown, jerky.
Posts: 8,353
Received 1,375 Likes
on
1,027 Posts

For torquing....I (me) have been having excellent and repeatable results on multiple S2000's using:
-"Polish" the hub face that the nut touches using a drill and wire wheel
-Clean axle threads and nut face with wire wheel
-EP grease on threads AND face
-250LB-FT of constantly swinging torque
Axle splines and hub splines also need to be smooth and greased.
Ironically enough, even though I did this via calculation...it happens to result in original stake + 50-60deg on most cars.
It doesn't even require me to get a pole and stick it on a semi-truck wrench and show my neighbours how crazy I am.
I'll caution that this is still technically/theoretically too much loading (which is why Honda doesn't do it this way). But...having luck thus far. No clicks and no breaks.
-"Polish" the hub face that the nut touches using a drill and wire wheel
-Clean axle threads and nut face with wire wheel
-EP grease on threads AND face
-250LB-FT of constantly swinging torque
Axle splines and hub splines also need to be smooth and greased.
Ironically enough, even though I did this via calculation...it happens to result in original stake + 50-60deg on most cars.
It doesn't even require me to get a pole and stick it on a semi-truck wrench and show my neighbours how crazy I am.
I'll caution that this is still technically/theoretically too much loading (which is why Honda doesn't do it this way). But...having luck thus far. No clicks and no breaks.
#13
Moderator



Greased threads will change the torque dramatically. In your case, you are likely right where this nut needs to be, estimated 350 ft-lb range if the nut threads were dry, and only the nut face was greased.
A dry 250 ft-lbs will not be sufficient to keep the bearing races from shifting on the hub. Does you procedure equate to approximately 60 degrees tighter than stock?
A dry 250 ft-lbs will not be sufficient to keep the bearing races from shifting on the hub. Does you procedure equate to approximately 60 degrees tighter than stock?
#14


Join Date: Nov 2007
Location: Illnoise. WAY downtown, jerky.
Posts: 8,353
Received 1,375 Likes
on
1,027 Posts

Greased threads will change the torque dramatically. In your case, you are likely right where this nut needs to be, estimated 350 ft-lb range if the nut threads were dry, and only the nut face was greased.
A dry 250 ft-lbs will not be sufficient to keep the bearing races from shifting on the hub. Does you procedure equate to approximately 60 degrees tighter than stock?
A dry 250 ft-lbs will not be sufficient to keep the bearing races from shifting on the hub. Does you procedure equate to approximately 60 degrees tighter than stock?
Greasing does increase the tension effect of torque...which is what you're after. It also makes that relationship MUCH more consistent than using a dry thread since the friction is controlled by the grease rather than relying on individual fastener surface conditions, environmental conditons, etc.
Grease equalizes a lot of variables....which is why precision bolts that do call a torque spec are spec'd with "wet" torque.
I'm sure you know all this. Just mentioning it for the greater good.
#16

I greased the stub and nut face and threads, didn't bother staking it, used whiteout to see if the nut would back off without staking. That was last November, the nut hasn't moved. I used a 3/4 in breaker bar to tighten them, didn't use a torque wrench at all, just cranked down on the nut until I couldn't lift any more, with the car in 6th and the parking brake on as far as I could pull it. The nut has not moved 1mm on either side, I didn't bother staking either in case I had to remove the axle again for whatever reason as I didn't want to wait for a new nut to arrive by mail. Should I stake them anyway?
I don't have any clunking or wheel bearing noise on my Doorman hubs and OEM bearings which are still going strong after 7* years.
The reason I used new nuts is because my axle would clunk when I reused the staked nuts, using brand new Honda axle nuts stopped the clunking.
Reason I pulled the axles was to swap in cups from two used passenger side axles since both my cups were pitted and had already been swapped side to side. I may have been lucky with my choice but both axle cups were prestine and I got a bunch of spare parts like bearings etc.
As far as I know, correct me if I'm wrong, launching the car from a stop does the damage to the axle cups, and causes the wheel bearing race to shift if the axle nut is not tight enough, that's what causes the tripod bearings to dig into the cups. Again, feel free to correct me if I'm wrong.
I don't have any clunking or wheel bearing noise on my Doorman hubs and OEM bearings which are still going strong after 7* years.
The reason I used new nuts is because my axle would clunk when I reused the staked nuts, using brand new Honda axle nuts stopped the clunking.
Reason I pulled the axles was to swap in cups from two used passenger side axles since both my cups were pitted and had already been swapped side to side. I may have been lucky with my choice but both axle cups were prestine and I got a bunch of spare parts like bearings etc.
As far as I know, correct me if I'm wrong, launching the car from a stop does the damage to the axle cups, and causes the wheel bearing race to shift if the axle nut is not tight enough, that's what causes the tripod bearings to dig into the cups. Again, feel free to correct me if I'm wrong.
#17


Join Date: Nov 2007
Location: Illnoise. WAY downtown, jerky.
Posts: 8,353
Received 1,375 Likes
on
1,027 Posts

^&The issue with the nut being loose OR too tight is that its not clamping the bearing to the hub properly.
I make explaining....
The nut is using the axle stub as a strong spring. The goal us to torque the nut till you have enough spring pre-tension on the stub to hold it together AND not allow it to excessively move during loading. That's the basic job of any fastener.
in more depth
The stub has to clamp all the parts together AND also hold everything from pulling apart during heavy cornering.
In a hard corner, the road pushes sideways on the tyre. The wheel and tyre are a lever arm. That lever is trying to pull the hub out of the bearing. The nut is using the stub as a pre-tensioner to prevent that movement.
Meaning stub needs to have enough stretch left in it to hold the parts together during loading too.
Which is why you need a torque setting that pre-tensions it about 75% lower than the yield point of the stub. And this is why you don't OVER torque the nut.
**75% is just an industry standard. Doesn't mean its correct for every application. Which is why there are a million different torque spec in the FSM, for the same sized bolts.**
If you torque the nut too much...it will yield the stud (permanently deform). If it yields, it won't hold any additonal tension. You've basically stretched the "spring" past its limit and now it's not pulling back any harder.
If you yielded it...and load it up on a hard corner...it doesn't have any strength left in it to pull back. So the force just stretches the stub more and allows the hub to come off the bearing slightly (same as if it was loose). And maybe snaps the stub.
If it snaps (people have seen them snap whilst driving), there is nothing but a press fit holding the hub to the bearing. The hub and wheel will come off if the friction fit slips.
That is why Honda does a very conservative torque. They would rather have a worn out bearing than a wheel and hub come off a car.
The 250LB greased setting I described is going to put significantly more tension on the stub than the Honda procedure. I'm using grease to lower the thread and face friction...so my wrench turns the nut further with the same torque setting.
I based my torque on a fairly conservative calculation. So...it should be fine.
As far as the cup wear goes..
Of course launching doesn't help anything. But the issue affects cars that haven't been launched.
Lowering a car is going to cause the bearings to have a bigger sweep inside the cup. The axle angle changes. Bigger sweep is needed at the bearing, since the diff flange is fixed. Bigger sweep delta in the same timespan = faster linear speed = more heat = more wear. Theoretically.
Highway driving also causes a constantly fast sweep and a constant torque. This theoretically
would also wear the axles out faster. Especially if combined with a bigger angle/longer sweep.
I am a proponent of using a better grease to help with the issue.
Redline CV2 is technically the wrong grease. BUT it does seem to work. A NLG1 1 is technically the right choice because of the roller bearings inside the main bearings.
I make explaining....
The nut is using the axle stub as a strong spring. The goal us to torque the nut till you have enough spring pre-tension on the stub to hold it together AND not allow it to excessively move during loading. That's the basic job of any fastener.
in more depth
The stub has to clamp all the parts together AND also hold everything from pulling apart during heavy cornering.
In a hard corner, the road pushes sideways on the tyre. The wheel and tyre are a lever arm. That lever is trying to pull the hub out of the bearing. The nut is using the stub as a pre-tensioner to prevent that movement.
Meaning stub needs to have enough stretch left in it to hold the parts together during loading too.
Which is why you need a torque setting that pre-tensions it about 75% lower than the yield point of the stub. And this is why you don't OVER torque the nut.
**75% is just an industry standard. Doesn't mean its correct for every application. Which is why there are a million different torque spec in the FSM, for the same sized bolts.**
If you torque the nut too much...it will yield the stud (permanently deform). If it yields, it won't hold any additonal tension. You've basically stretched the "spring" past its limit and now it's not pulling back any harder.
If you yielded it...and load it up on a hard corner...it doesn't have any strength left in it to pull back. So the force just stretches the stub more and allows the hub to come off the bearing slightly (same as if it was loose). And maybe snaps the stub.
If it snaps (people have seen them snap whilst driving), there is nothing but a press fit holding the hub to the bearing. The hub and wheel will come off if the friction fit slips.
That is why Honda does a very conservative torque. They would rather have a worn out bearing than a wheel and hub come off a car.
The 250LB greased setting I described is going to put significantly more tension on the stub than the Honda procedure. I'm using grease to lower the thread and face friction...so my wrench turns the nut further with the same torque setting.
I based my torque on a fairly conservative calculation. So...it should be fine.
As far as the cup wear goes..
Of course launching doesn't help anything. But the issue affects cars that haven't been launched.
Lowering a car is going to cause the bearings to have a bigger sweep inside the cup. The axle angle changes. Bigger sweep is needed at the bearing, since the diff flange is fixed. Bigger sweep delta in the same timespan = faster linear speed = more heat = more wear. Theoretically.
Highway driving also causes a constantly fast sweep and a constant torque. This theoretically
would also wear the axles out faster. Especially if combined with a bigger angle/longer sweep.
I am a proponent of using a better grease to help with the issue.
Redline CV2 is technically the wrong grease. BUT it does seem to work. A NLG1 1 is technically the right choice because of the roller bearings inside the main bearings.
The following users liked this post:
Slowcrash_101 (04-27-2021)
#18

^&The issue with the nut being loose OR too tight is that its not clamping the bearing to the hub properly.
I make explaining....
The nut is using the axle stub as a strong spring. The goal us to torque the nut till you have enough spring pre-tension on the stub to hold it together AND not allow it to excessively move during loading. That's the basic job of any fastener.
in more depth
The stub has to clamp all the parts together AND also hold everything from pulling apart during heavy cornering.
In a hard corner, the road pushes sideways on the tyre. The wheel and tyre are a lever arm. That lever is trying to pull the hub out of the bearing. The nut is using the stub as a pre-tensioner to prevent that movement.
Meaning stub needs to have enough stretch left in it to hold the parts together during loading too.
Which is why you need a torque setting that pre-tensions it about 75% lower than the yield point of the stub. And this is why you don't OVER torque the nut.
**75% is just an industry standard. Doesn't mean its correct for every application. Which is why there are a million different torque spec in the FSM, for the same sized bolts.**
If you torque the nut too much...it will yield the stud (permanently deform). If it yields, it won't hold any additonal tension. You've basically stretched the "spring" past its limit and now it's not pulling back any harder.
If you yielded it...and load it up on a hard corner...it doesn't have any strength left in it to pull back. So the force just stretches the stub more and allows the hub to come off the bearing slightly (same as if it was loose). And maybe snaps the stub.
If it snaps (people have seen them snap whilst driving), there is nothing but a press fit holding the hub to the bearing. The hub and wheel will come off if the friction fit slips.
That is why Honda does a very conservative torque. They would rather have a worn out bearing than a wheel and hub come off a car.
The 250LB greased setting I described is going to put significantly more tension on the stub than the Honda procedure. I'm using grease to lower the thread and face friction...so my wrench turns the nut further with the same torque setting.
I based my torque on a fairly conservative calculation. So...it should be fine.
As far as the cup wear goes..
Of course launching doesn't help anything. But the issue affects cars that haven't been launched.
Lowering a car is going to cause the bearings to have a bigger sweep inside the cup. The axle angle changes. Bigger sweep is needed at the bearing, since the diff flange is fixed. Bigger sweep delta in the same timespan = faster linear speed = more heat = more wear. Theoretically.
Highway driving also causes a constantly fast sweep and a constant torque. This theoretically
would also wear the axles out faster. Especially if combined with a bigger angle/longer sweep.
I am a proponent of using a better grease to help with the issue.
Redline CV2 is technically the wrong grease. BUT it does seem to work. A NLG1 1 is technically the right choice because of the roller bearings inside the main bearings.
I make explaining....
The nut is using the axle stub as a strong spring. The goal us to torque the nut till you have enough spring pre-tension on the stub to hold it together AND not allow it to excessively move during loading. That's the basic job of any fastener.
in more depth
The stub has to clamp all the parts together AND also hold everything from pulling apart during heavy cornering.
In a hard corner, the road pushes sideways on the tyre. The wheel and tyre are a lever arm. That lever is trying to pull the hub out of the bearing. The nut is using the stub as a pre-tensioner to prevent that movement.
Meaning stub needs to have enough stretch left in it to hold the parts together during loading too.
Which is why you need a torque setting that pre-tensions it about 75% lower than the yield point of the stub. And this is why you don't OVER torque the nut.
**75% is just an industry standard. Doesn't mean its correct for every application. Which is why there are a million different torque spec in the FSM, for the same sized bolts.**
If you torque the nut too much...it will yield the stud (permanently deform). If it yields, it won't hold any additonal tension. You've basically stretched the "spring" past its limit and now it's not pulling back any harder.
If you yielded it...and load it up on a hard corner...it doesn't have any strength left in it to pull back. So the force just stretches the stub more and allows the hub to come off the bearing slightly (same as if it was loose). And maybe snaps the stub.
If it snaps (people have seen them snap whilst driving), there is nothing but a press fit holding the hub to the bearing. The hub and wheel will come off if the friction fit slips.
That is why Honda does a very conservative torque. They would rather have a worn out bearing than a wheel and hub come off a car.
The 250LB greased setting I described is going to put significantly more tension on the stub than the Honda procedure. I'm using grease to lower the thread and face friction...so my wrench turns the nut further with the same torque setting.
I based my torque on a fairly conservative calculation. So...it should be fine.
As far as the cup wear goes..
Of course launching doesn't help anything. But the issue affects cars that haven't been launched.
Lowering a car is going to cause the bearings to have a bigger sweep inside the cup. The axle angle changes. Bigger sweep is needed at the bearing, since the diff flange is fixed. Bigger sweep delta in the same timespan = faster linear speed = more heat = more wear. Theoretically.
Highway driving also causes a constantly fast sweep and a constant torque. This theoretically
would also wear the axles out faster. Especially if combined with a bigger angle/longer sweep.
I am a proponent of using a better grease to help with the issue.
Redline CV2 is technically the wrong grease. BUT it does seem to work. A NLG1 1 is technically the right choice because of the roller bearings inside the main bearings.
John Deere poly grease and Lucas Xtra heavy duty are good replacements, Mobil 1 is fine as well, and CV2 is fine but you have to really clean out the old grease. CV2 and the OEM poly grease are not compatible. It will thin out the cv2 grease if you aren't thorough.
#19

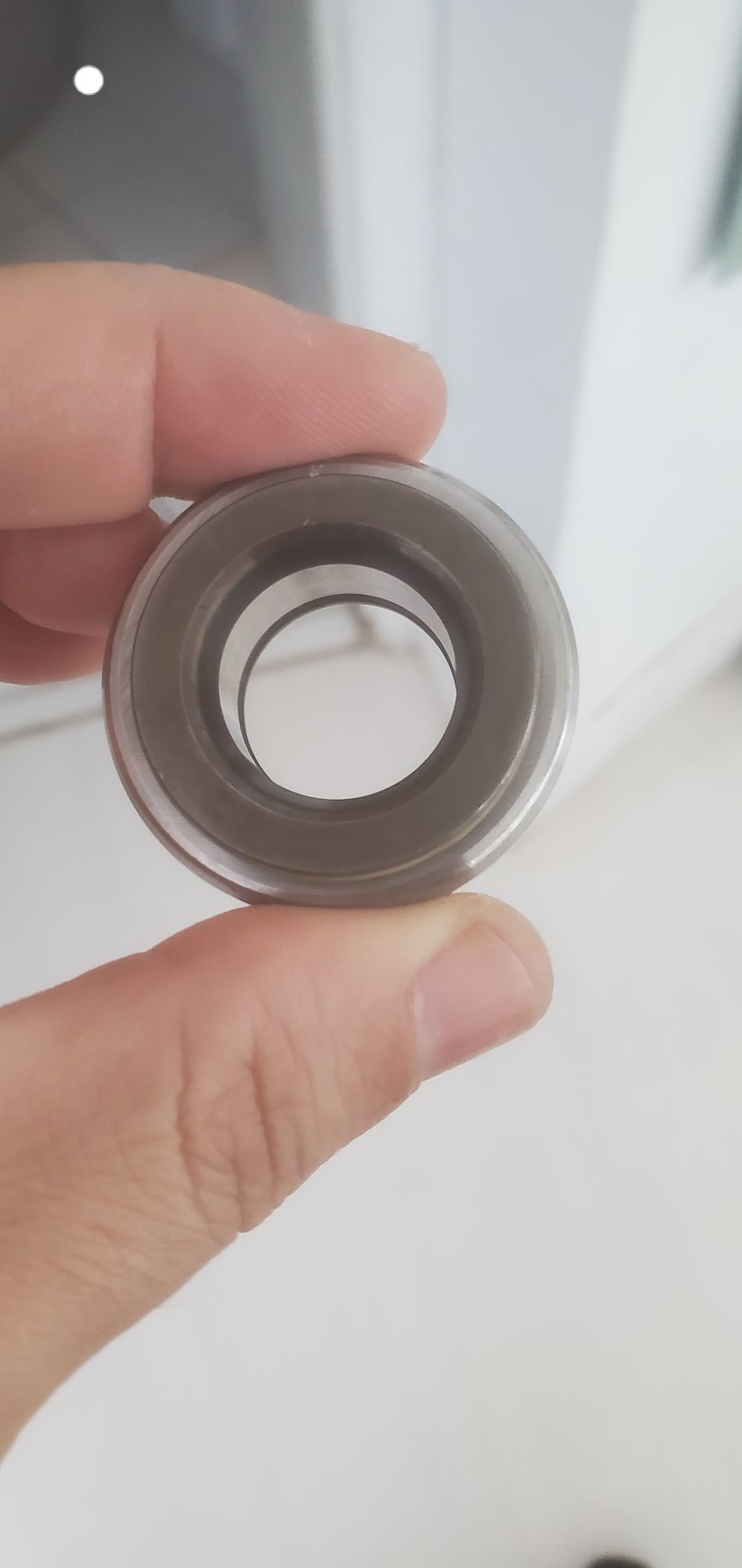
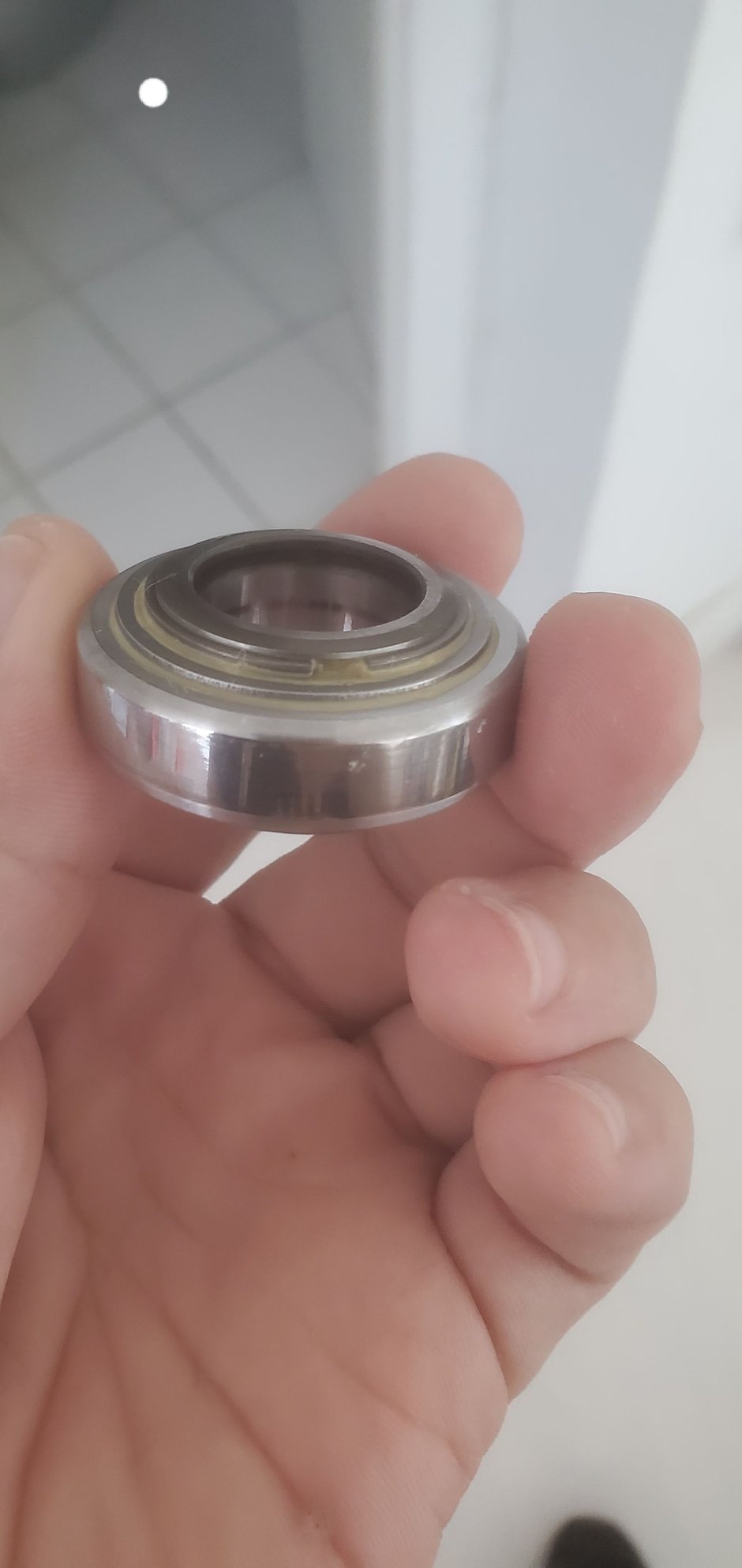
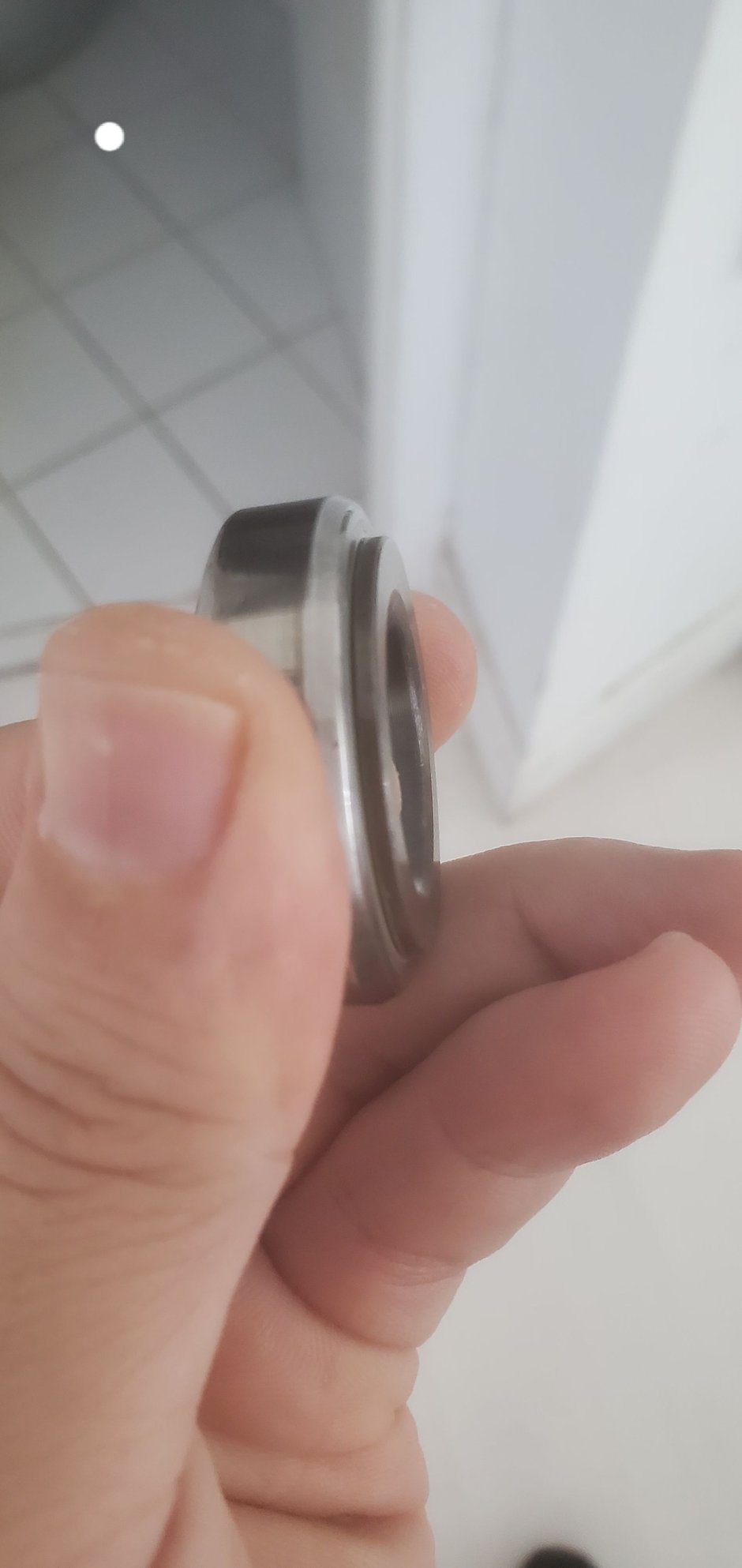
Here is one of the roller bearings of the tripod. There is two ways for grease to get in and out. I soaked it in acetone for 20 minutes but it did nothing to the grease hiding inside.
How would I go about separating this bearing? For science.
On the second pic you can see a gap that allows grease in, the back side has a little play exposing a small gap, I imagine grease cycles through there as well.
There's a fair bit of heat scoring on the bearing where it sits on the tripod.
Still rolls smooth as butter, no noise at all.