Oil return line fitting
#11

Originally Posted by Torque Obsessed,Jul 20 2010, 10:45 AM
If the turbo is higher then the oil level in the pan, gravity will drain it fine. The oil doesn't have to "fall" out of the line into the pan for it to drain.
and when we did the testing on the return lines with a clear drain tube, excessive flow was not an issue what so ever.
#13

Wow Lots of responses......
I had the welder "fix" it. I haven't gone too pick it up yet but he says he fixed it. So we'll see in a few hrs.
This would have been my preferred method. But unfortunately I'm working with some time constraints at this point in the game. The bottom end of the engine never came out of the vehicle & tapping the girdle can be a difficult task with the block still in the car.
[QUOTE]Every person and the professional shops (Inline-Mase) have mixed Opinion on where to put the oil return .
I had the welder "fix" it. I haven't gone too pick it up yet but he says he fixed it. So we'll see in a few hrs.
tap the girdle, even the top of the pan will back up
[QUOTE]Every person and the professional shops (Inline-Mase) have mixed Opinion on where to put the oil return .
#14
Registered User
Join Date: Jan 2008
Location: Lakeland, Florida
Posts: 1,967
Likes: 0
Received 0 Likes
on
0 Posts

^i dont know how much is actually cycling in the motor and turbo when running. thats why i gave high to low hypthetical lines. it would be stricly a guess bro.
as for the fitting. where people crack me up with line sizing is ID continuance. yeah, maybe you have a 3/4" diameter return hose, but with your fittings, the ID of them restricts it down. and the smallest diameter of the entire return line(whether it be in the very begining, end or middle) is the largest amount it can flow. fittings play and important role. take some of those and measure their ID in comparison to your line. they arnt always smaller, but 75% of the time i bet they are.
so when i say i run a 5/8" ID line, everything from the square outlet on the turbo to the bored hole in the pan is 5/8" ID.
also, the return is not so much pressurized. it comes out of the turbo with a tiny bit of force, but nothing worth noting. gravity and a continuous diameter return is the best.
here are some pics of how i did my pan, and sort description of the method:



i took a piece of 1&1/4" aluminum round stock. bored it to 5/8", then bored and tapped the end for the 1/2"NPT fitting(the ID of the entire fitting was 5/8"). then found the closest to straight angle leading to the turbo and welded the tube to the highest spot on the pan above where the oil sat at OEM tilt. this way, it is like a straight shot into the pan of un-interrupted flow. and any area that might get oil into the fitting or line is now a solid welded aluminum bar that will not leak since the fitting is above the top of the oil pan. taking into account the slosh from some decent cornering ;-)
hope this helps.
longest post ever, i know. lol
as for the fitting. where people crack me up with line sizing is ID continuance. yeah, maybe you have a 3/4" diameter return hose, but with your fittings, the ID of them restricts it down. and the smallest diameter of the entire return line(whether it be in the very begining, end or middle) is the largest amount it can flow. fittings play and important role. take some of those and measure their ID in comparison to your line. they arnt always smaller, but 75% of the time i bet they are.
so when i say i run a 5/8" ID line, everything from the square outlet on the turbo to the bored hole in the pan is 5/8" ID.
also, the return is not so much pressurized. it comes out of the turbo with a tiny bit of force, but nothing worth noting. gravity and a continuous diameter return is the best.
here are some pics of how i did my pan, and sort description of the method:



i took a piece of 1&1/4" aluminum round stock. bored it to 5/8", then bored and tapped the end for the 1/2"NPT fitting(the ID of the entire fitting was 5/8"). then found the closest to straight angle leading to the turbo and welded the tube to the highest spot on the pan above where the oil sat at OEM tilt. this way, it is like a straight shot into the pan of un-interrupted flow. and any area that might get oil into the fitting or line is now a solid welded aluminum bar that will not leak since the fitting is above the top of the oil pan. taking into account the slosh from some decent cornering ;-)
hope this helps.
longest post ever, i know. lol
#15

nice idea! i was thinking of doing something like that but using a block cut an an angle. basicly the same idea but i guess your way will still have the hole higher than the way i was thinking of doing it. but in the end i got lazy

#16

Originally Posted by teamvalorracing,Jul 21 2010, 08:01 AM
^i dont know how much is actually cycling in the motor and turbo when running. thats why i gave high to low hypthetical lines. it would be stricly a guess bro.
as for the fitting. where people crack me up with line sizing is ID continuance. yeah, maybe you have a 3/4" diameter return hose, but with your fittings, the ID of them restricts it down. and the smallest diameter of the entire return line(whether it be in the very begining, end or middle) is the largest amount it can flow. fittings play and important role. take some of those and measure their ID in comparison to your line. they arnt always smaller, but 75% of the time i bet they are.
so when i say i run a 5/8" ID line, everything from the square outlet on the turbo to the bored hole in the pan is 5/8" ID.
also, the return is not so much pressurized. it comes out of the turbo with a tiny bit of force, but nothing worth noting. gravity and a continuous diameter return is the best.
here are some pics of how i did my pan, and sort description of the method
i took a piece of 1&1/4" aluminum round stock. bored it to 5/8", then bored and tapped the end for the 1/2"NPT fitting(the ID of the entire fitting was 5/8"). then found the closest to straight angle leading to the turbo and welded the tube to the highest spot on the pan above where the oil sat at OEM tilt. this way, it is like a straight shot into the pan of un-interrupted flow. and any area that might get oil into the fitting or line is now a solid welded aluminum bar that will not leak since the fitting is above the top of the oil pan. taking into account the slosh from some decent cornering ;-)
hope this helps.
longest post ever, i know. lol
as for the fitting. where people crack me up with line sizing is ID continuance. yeah, maybe you have a 3/4" diameter return hose, but with your fittings, the ID of them restricts it down. and the smallest diameter of the entire return line(whether it be in the very begining, end or middle) is the largest amount it can flow. fittings play and important role. take some of those and measure their ID in comparison to your line. they arnt always smaller, but 75% of the time i bet they are.
so when i say i run a 5/8" ID line, everything from the square outlet on the turbo to the bored hole in the pan is 5/8" ID.
also, the return is not so much pressurized. it comes out of the turbo with a tiny bit of force, but nothing worth noting. gravity and a continuous diameter return is the best.
here are some pics of how i did my pan, and sort description of the method
i took a piece of 1&1/4" aluminum round stock. bored it to 5/8", then bored and tapped the end for the 1/2"NPT fitting(the ID of the entire fitting was 5/8"). then found the closest to straight angle leading to the turbo and welded the tube to the highest spot on the pan above where the oil sat at OEM tilt. this way, it is like a straight shot into the pan of un-interrupted flow. and any area that might get oil into the fitting or line is now a solid welded aluminum bar that will not leak since the fitting is above the top of the oil pan. taking into account the slosh from some decent cornering ;-)
hope this helps.
longest post ever, i know. lol
I donno why it was so hard for the people I paid to do my work didn't put an inch out thought into it.
Well the guy finally dropped the pan off too me this time. Instead of having to drive out and pick it up. I still think he did horrible work tho. Not to mention his bad attitude about having to do it over and accusing me of not being specific.
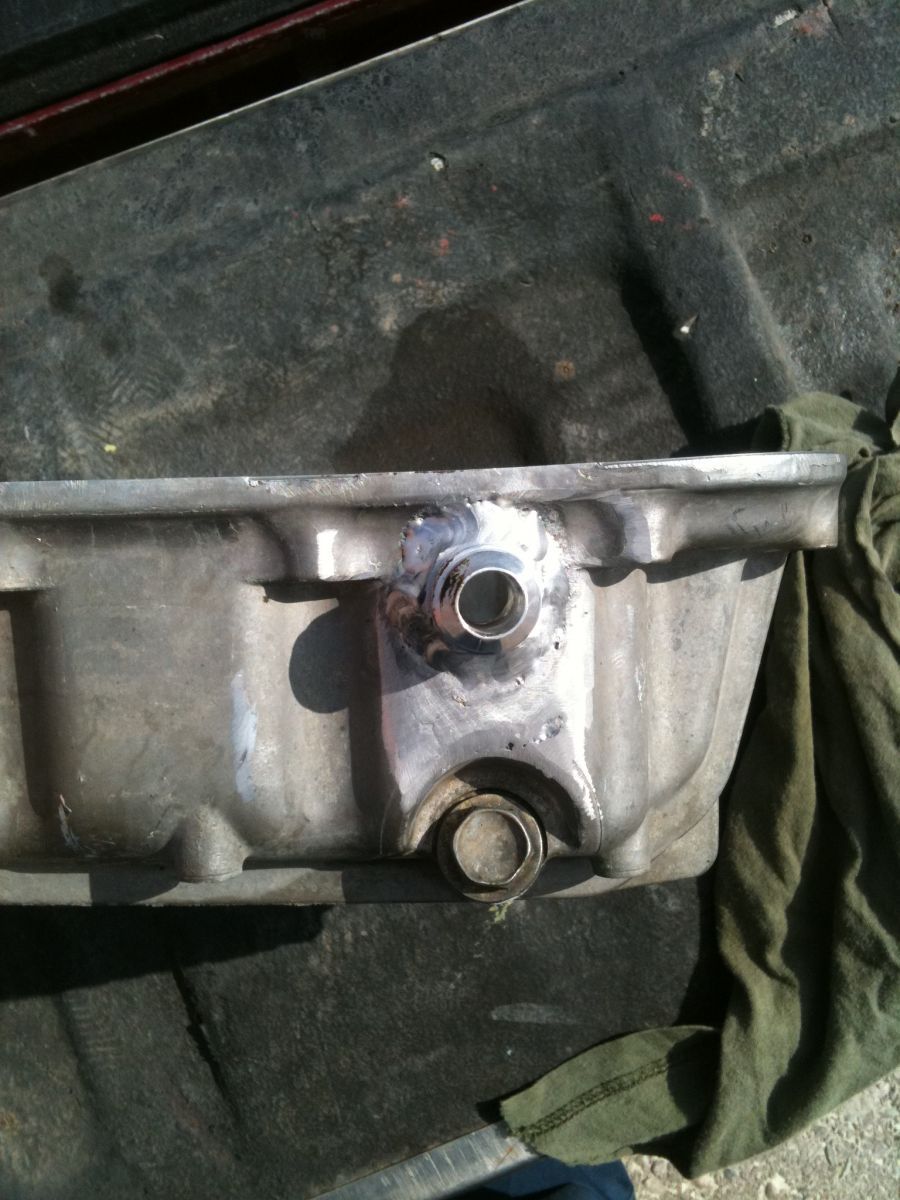
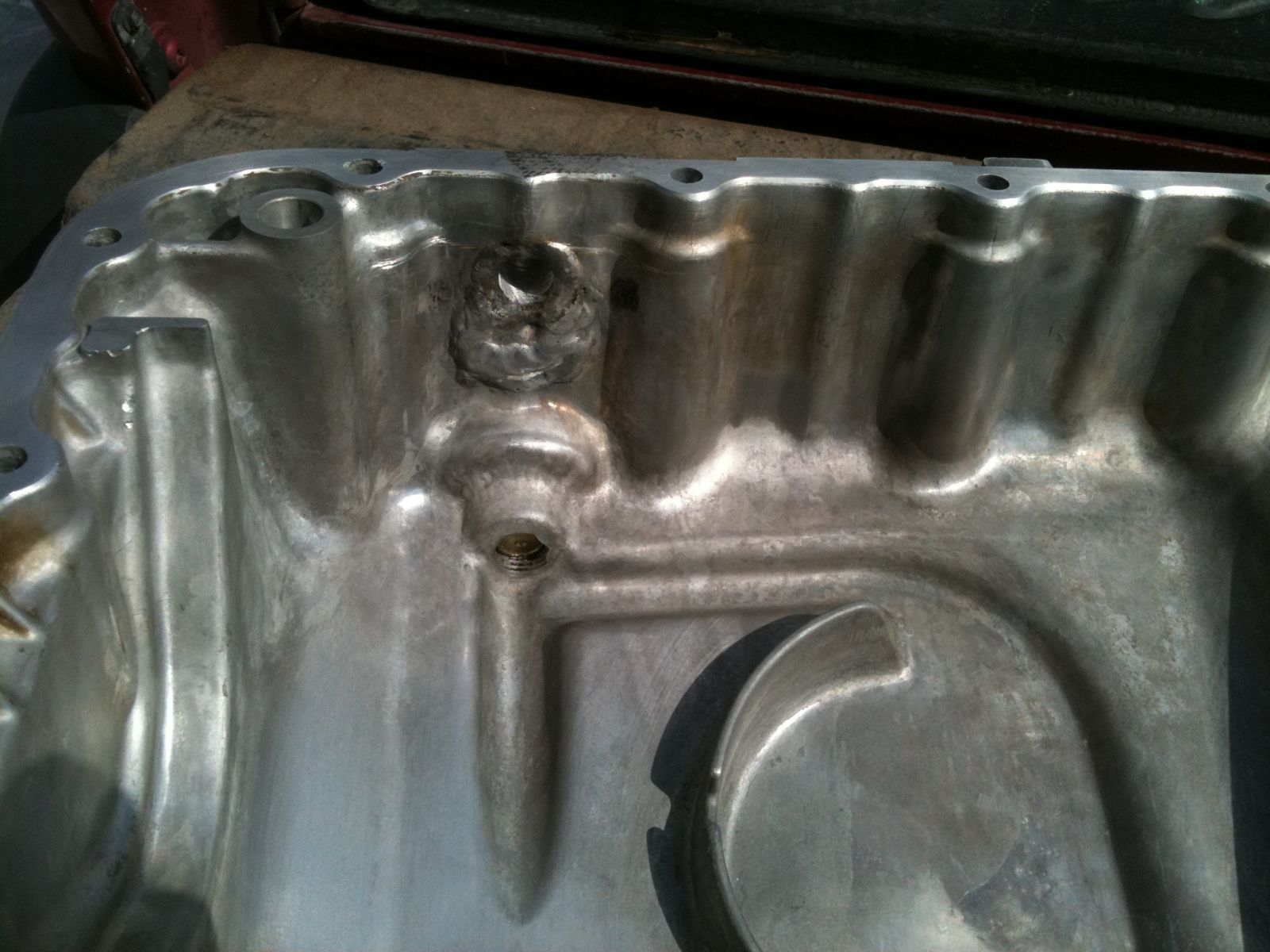
Still a hack job IMHO. I just wanted to be done with them after this. The guy doing the work had the nerve to say I was being a prick about this.
Maximum Horsepower Machine in Gilbert, AZ gets ZERO stars for horrible customer service @ just plain bad workmanship.
Thread
Thread Starter
Forum
Replies
Last Post
kkyntmoon
New York - Metro New York S2000 Owners
3
01-21-2008 03:54 AM